Welding involves more than just joining two pieces of metal together, its practice is based on science and research – particularly understanding materials and their properties.
The science of metals is commonly referred to as ‘metallurgy’, which focuses on the production and purification of certain materials. Progress in metallurgy in the second half of the twentieth century was associated with rapid replacement of the basic production systems, that can be described as a technical revolution. The science of welding is referred to as welding metallurgy, and deals with the behaviour of metals subject to welding.
In the past decade, progress in ferrous metallurgy (the science of iron-based alloys such as carbon steels and stainless steels) has been characterised primarily by the development of nanotechnologies—in particular, the production of high-quality materials used in electronics, optics, construction, the power industry, manufacturing, astronautics, and elsewhere.
Importantly, metallurgical processes have changed throughout history, and today the process of manufacturing heavily relies on welding metallurgy that is cost effective and environmentally sustainable.
Industry Supported By Scientific Research
Metallurgical research has expanded across Australia, producing thousands of jobs and economic prosperity for the sector. This growth has been underpinned by Australian universities and other education providers who are at the forefront of technical innovations for industry.
In Victoria alone, metallurgy research is being led at Monash and Deakin Universities. At Monash University, researchers and engineers have spent time working with companies like ArcelorMittal – the world’s biggest steel company – to advance steel manufacturing for automotive products.
The technical innovations in this area are delivering stronger steel, which allows car manufacturers to use less steel in car components. Together, the parts are lighter, which reduces fuel emissions.
Similarly, over 200 researchers at Deakin University have worked on materials science and engineering at the Institute for Frontier Materials. The team continue to learn about welding and metallurgical processes to ensure battery materials have another life after the device becomes redundant.
The RMIT $35 million Centre for Additive Manufacturing in Victoria, boasts one of Australia’s largest 3D printing facilities. The Centre develops new materials and design tools to boost Australia’s 3D printing capabilities, and take the welding industry from strength to strength.
The Centre has already explored laser technologies, which can repair existing welded components and in addition, to refurbish worn out or damaged component surfaces through a process called laser cladding. For example, parts for the Lockheed Martin F-35 Lightning II can be created to repair existing aircraft damage. These customised parts support a strong Australian-based manufacturing sector, which ensures jobs and opportunities are created for new apprentices.
Science also plays a critical role in the defence industry, where a TIP-TIG welding method – involving gas tungsten arc welding – is leading to improved efficiencies for submarines. ASC Shipbuilding is using these welding innovation expertise for submarine hull fabrication and other submarine welding roles.
Industry-Research Collaborations
The Australian welding industry is highly collaborative in nature, and its research and development institutes are no different. Across the country, there are several examples of programs designed to help foster industry-research collaborations that both advance research and develop outcomes and to solve challenges faced by industry.
Facility for Intelligent Fabrication
The Facility for Intelligent Fabrication (FIF) combines the knowledge and resources of the University of Wollongong (UOW), TAFE NSW and Weld Australia. FIF was formed in recognition of the changing business climate, as the Illawarra transitions from large-scale heavy manufacturing, and the need for local manufacturers to innovate and adapt to remain competitive.
The facility draws on decades of research-based welding and automation expertise and welding training at both UOW and TAFE NSW, enabling local firms with their own history of fabrication expertise to access specialised knowledge and skills in automation.
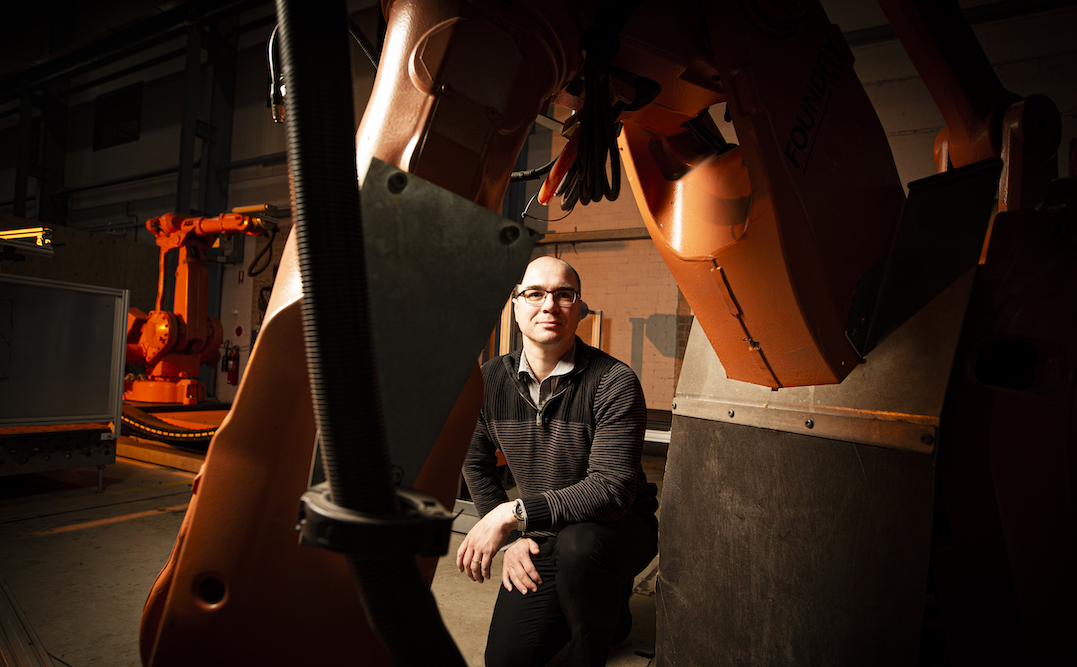
Advanced Robotics for Manufacturing Hub
A not-for-profit company with a mission to accelerate industry’s uptake of advanced manufacturing technologies and processes, the Advanced Robotics for Manufacturing (ARM) Hub is a collaboration between industry, research institutions, and government in Queensland.
The ARM Hub is bringing world-leading expertise in advanced robotics and design-led manufacturing to the aid of Australian businesses and their global supply chains. The Hub provides services to small-to-medium and micro-enterprise manufacturers, helping them become successful advanced manufacturing businesses. The Hub also collaborates with large companies to help drive digital transformation and support local supply chain development.
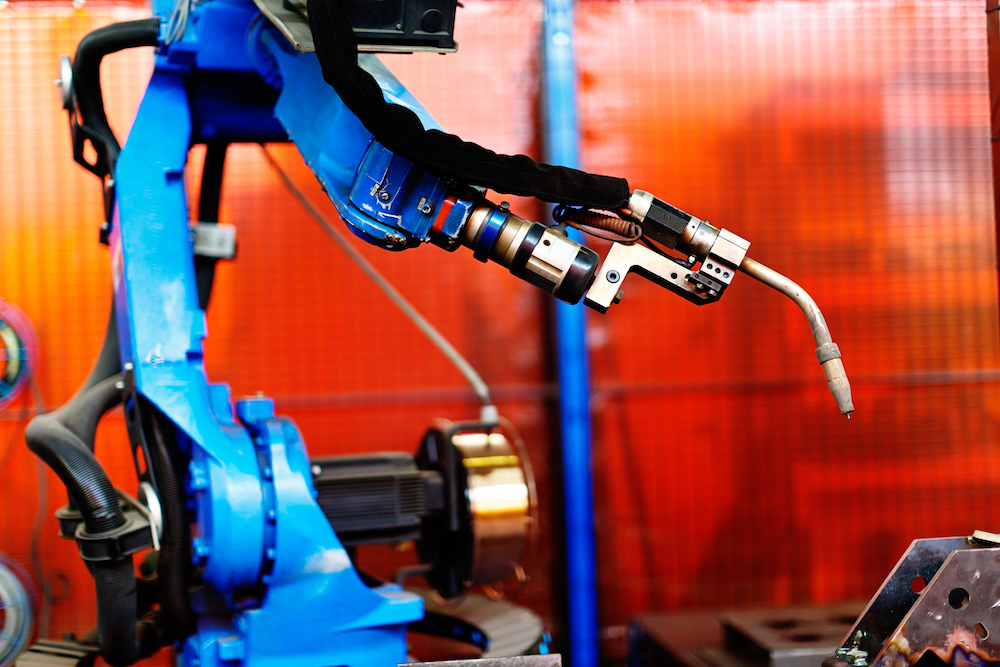
Further Information
If you would like more information about Weld Australia’s advocacy activities, please read our latest news and media releases. Alternatively, please feel free to contact us.